
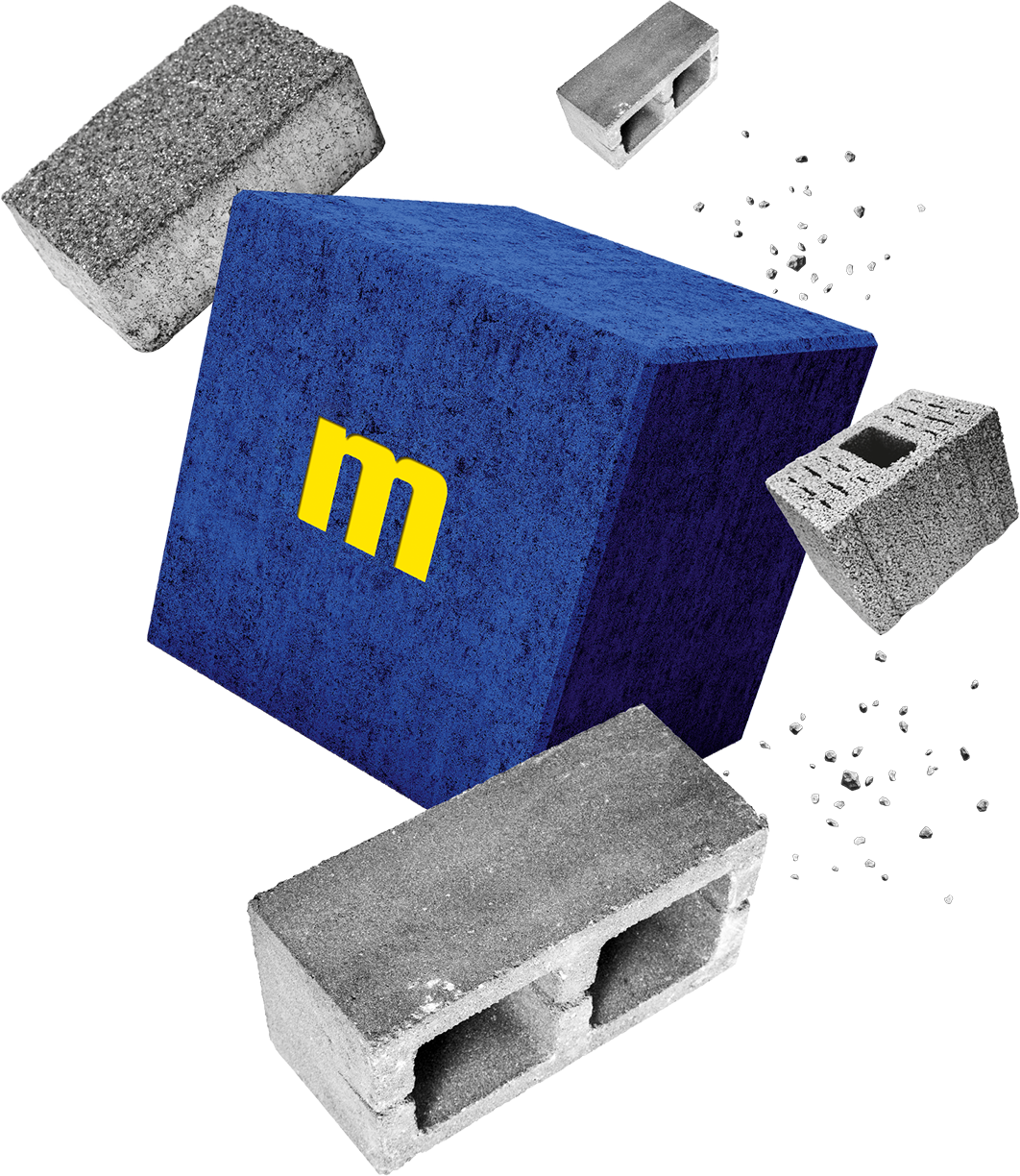
A perfect mould filling is the guarantee for quality and quantity.
Our milestones enable you to realise your individual product requirements.
On this page our Masa concrete heads present different solutions relating to the filling process.
At Masa, we think only concrete
... and how to shape it for the building materials industry. The machines we develop and manufacture are used for the production of kerbstones, concrete blocks and pavers, garden and landscaping products, sand-lime bricks and aerated concrete blocks and (reinforced) panels. In other words, we are real concrete heads with a passion for reliable machines.
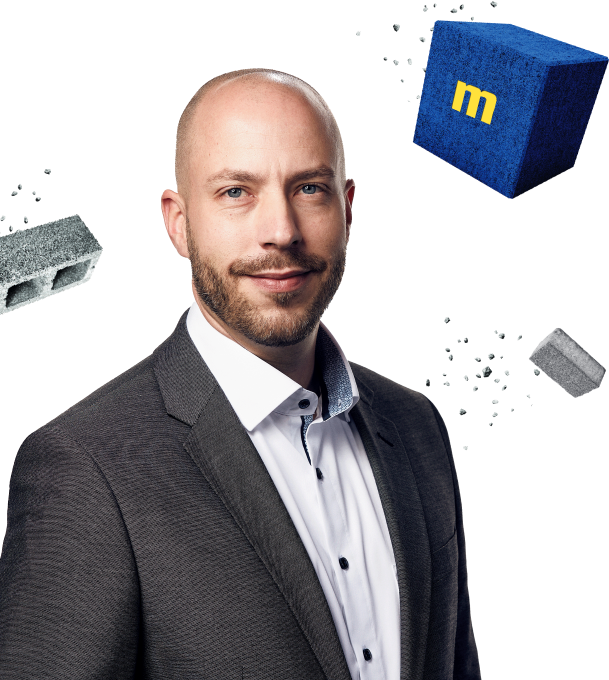
The concrete must be evenly distributed across the production board and, above all, into the narrow faceshells and webs.
“My milestone ensures that the concrete reaches even the smallest corner.”
Sven Luy is one of our smart concrete heads, whose daily business is the closeness to the customers with their individual product requirements.
You want to know more about our solutions for thin-walled products? Sign up for our bluepaper “It’s the filling that counts” or a personal appointment with one of our salesmen in your region.
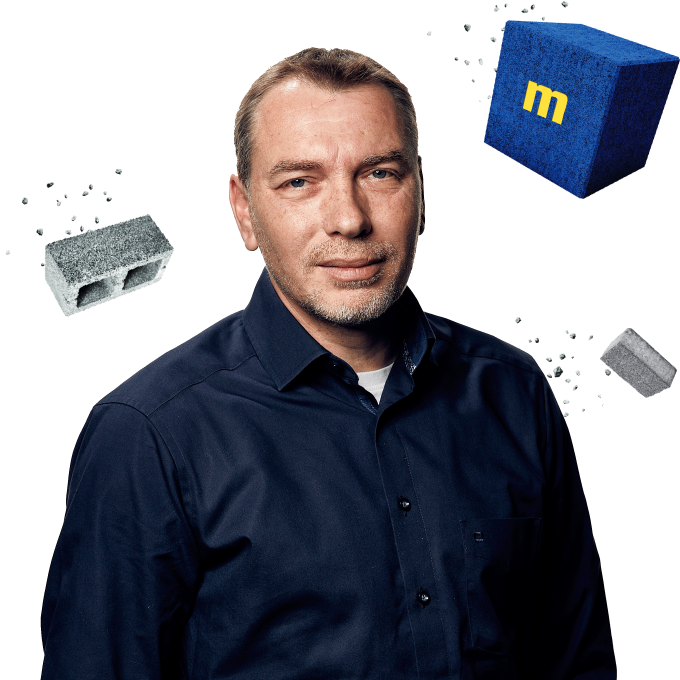
The filling box may not stock enough concrete to fill the mould completely evenly in one filling operation.
“My milestone enables you to achieve consistently high compaction even with large masses.”
Our smart concrete head, Karl-Josef Hauröder developed the symmetrical and torsionally rigid design of the proven, onepiece vibration table. The result is an even distribution of mass and an even input of impact energy when the impact bars bounce against the production board.
You want to know more about our solutions for large-volume concrete products? Sign up for our bluepaper “It’s the filling that counts” or a personal appointment with one of our salesmen in your region.
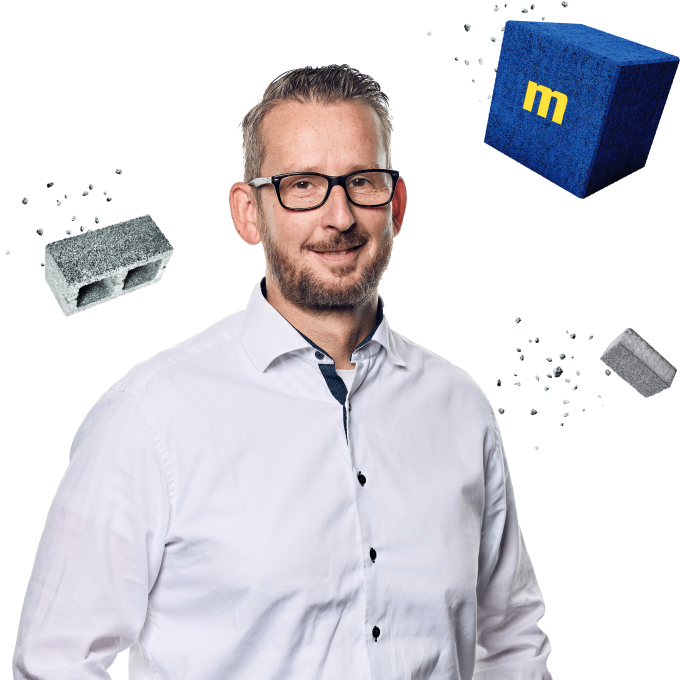
The market increasingly demands uniformly closed surfaces with high raw densities and strengths.
“My milestone offers you various possibilities to optimise your product in nuances to gain a competitive market lead with unique products.”
Our smart concrete head, Marc Reinert is very familiar with our range of special components that can be used to manage the fine-tuning of large-format concrete products and slabs. For example in the multi-colour production, our dosing slide minimises, among other things, the risk of undesired colour smears and increases the reproducibility of the product patterns.
You want to know more about our solutions for thin-walled products? Sign up for our bluepaper “It’s the filling that counts” or a personal appointment with one of our salesmen in your region.
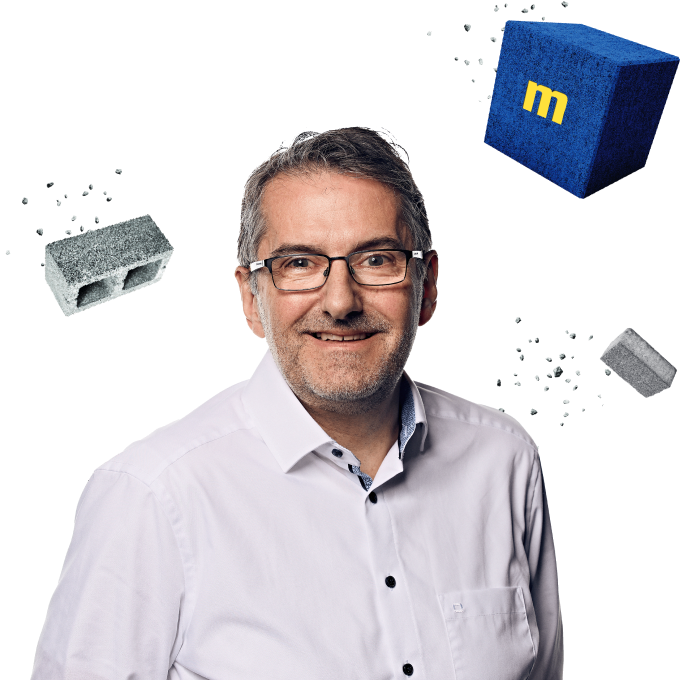
Pavers with sharp, highly sensitive edges require special handling. The demoulding process must be extremely uniform.
“My milestone enables you individual advice in selecting the most suitable components for your machine configuration to match your product requirements.”
Our smart concrete head, Rudolf Buyna, has many years of experience in advising customers that gives him the necessary instinct for selecting the right block making machine with its associated features. The fine tuning between the lower and upper mould parts is ensured by the mechanics (XL series) or servo-hydraulics (XL-R series). Depending on the characteristics of the paver edges, further equipment will be necessary.
You want to know more about our solutions for pavers with and without chamfer? Sign up for our bluepaper “It’s the filling that counts” or a personal appointment with one of our salesmen in your region
Highly efficient and
cycle time optimised.
Since we have designed this model series particularly for the requirements of the gardening and landscaping sectors as well as large products, we equip the Premium Line machines right from the start with many product and cycle time-oriented features for modern concrete block and paver production. The energy-efficient servo technologies we use should be specifically mentioned in this regard.
That is our XL-R:
- Servo hydraulics with hydraulic accumulators
- Mould bearing synchronisation via servo-controlled hydraulics
- Cycle time optimisation through:
• Intelligent drives
• Servo-controlled, fast feed of the production boards in combination with a synchronised V-belt lowering device
• Overlapping movements
• More energy-efficient drive systems - Set-up time optimisation through magnetic clamping of the filling box rails
- Laser-controlled level measurement in the filling box
- Larger configuration possibilities
- Extensive standard equipment
- Automation applications to support intuitive operation and reliable plant performance
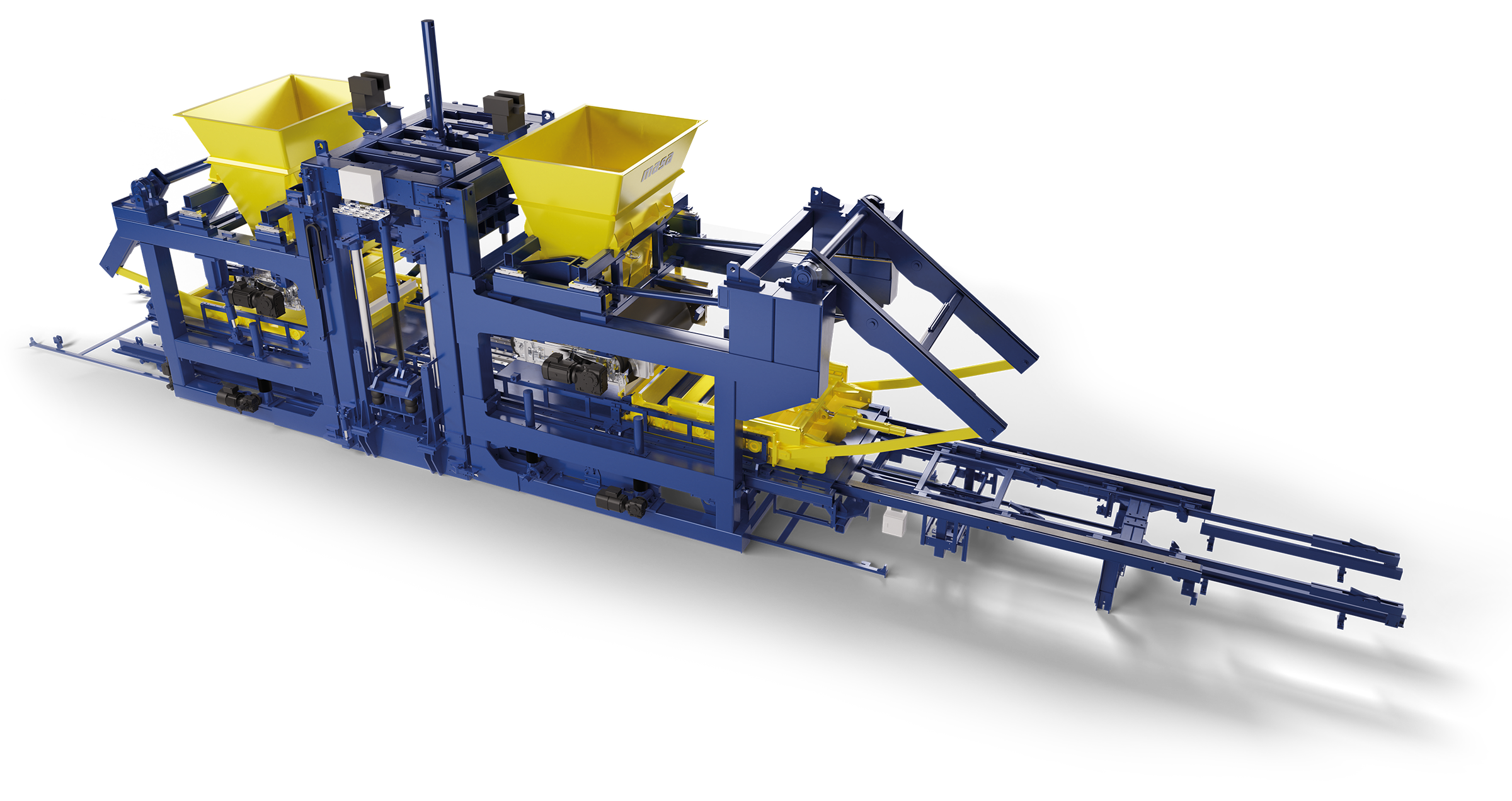
Subscribe to the newsletter for news and updates.
Download our bluepaper now!
You can find our different solutions relating to the filling process in our bluepaper “It’s the filling that counts”.
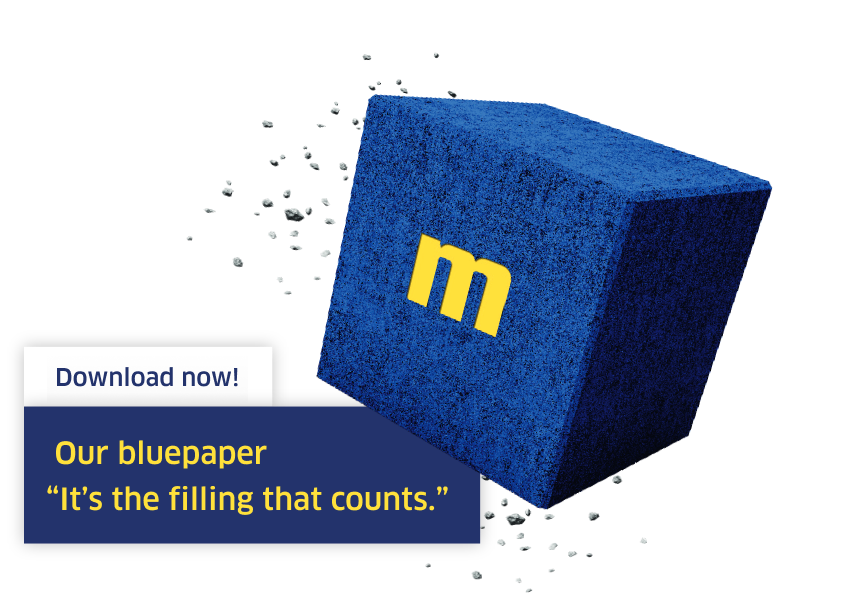